Производство кабин и двигателей для новых КамАЗов
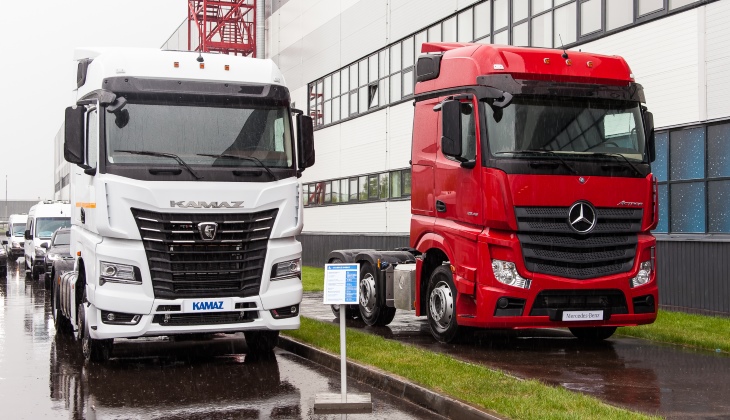
В конце мая в Набережных Челнах открыли завод совместного предприятия КамАЗа и «Даймлера», где производят каркасы кабин для грузовиков КамАЗ-54901 и Mercedes Actros. Производственная мощность завода — 55 тысяч кабин ежегодно, из которых 80% будут российскими моделями, а 20% — немецкими. Это соотношение может меняться в зависимости от потребностей партнеров.
Открытие предприятия прошло под девизом «Будущее уже здесь». Представители компании утверждают, что завод, заложенный в марте 2016 года, является самым современным и экологичным в мире. Инвестиции в завод составили около 200 миллионов евро, площадь его занимает 72 тысячи квадратных метров, он обеспечит работой до 700 человек при мощности в 55 тысяч кабин в год. К таким показателям планируется прийти к 2024 году.
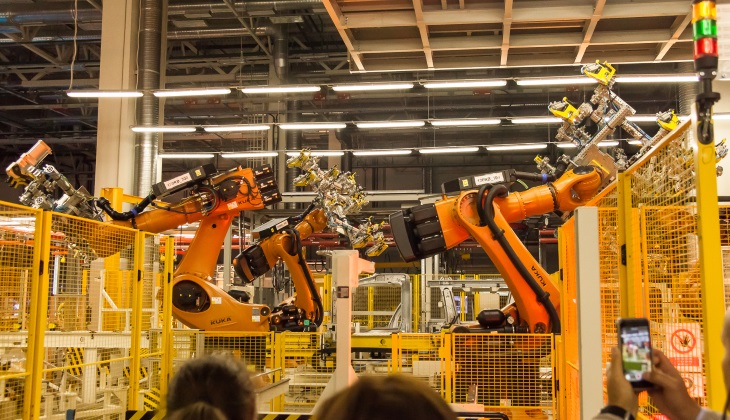
На заводе «трудятся» 106 роботов
Процесс начинается со склада деталей. Стеллажи располагаются максимально близко друг к другу, достаточно тесно, чтобы между ними проходил специальный погрузчик. Детали загружают на специальные самоходные тележки и транспортируют в кузовной цех. К слову, локализация даже сейчас весьма достойная. Представители компании отмечают, что в первую очередь стремились уйти от ввоза тех деталей, которым тяжело даётся транспортировка. Поэтому все видимые внешние кузовные детали уже производятся здесь. Сталь, из которой штампуются детали, также российская. Была проведена большая работа с поставщиками для того, чтобы она соответствовала всем высоким стандартам концерна Daimler.
В кузовной цех поступают детали, конфигурация которого напоминает рыбний хребет: центральная линия и детали с двух сторон. Помимо сварки в кабине используется склейка (клей подогревается до 48 градусов). Роботы KUKA выполняют все процессы под контролем компьютера. Качество сварки проверяется ультразвуком. Планируется уменьшить объемы проверки, отладки процессов и выхода на проектную мощность. Точность изготовления такая, что отклонение каждого размера собранного каркаса кабины (длины, ширины и высоты) от номинала не должно превышать 1,5 мм. При несоблюдении условия кабину направляют в лабораторию для тщательного обмера сканером с использованием оптики Zeiss.
Полученная трехмерная модель с цветовой индикацией (зеленый – хорошо, красный – плохо) отображается на мониторе. При подтверждении отклонений кабину признают непригодной и утилизируют, что случается очень редко. Даже отбраковка одной-двух кабин в год считается большим показателем при планируемых объёмах производства. Производство предусматривает разумную экономию: наконечники, которыми роботы сваривают детали, затупляются в процессе работы из-за увеличения площади контакта. Такие наконечники не выбрасывают, а заточивают (под компьютерным контролем) и снова устанавливают на робота. В итоге один наконечник можно использовать до трех раз.
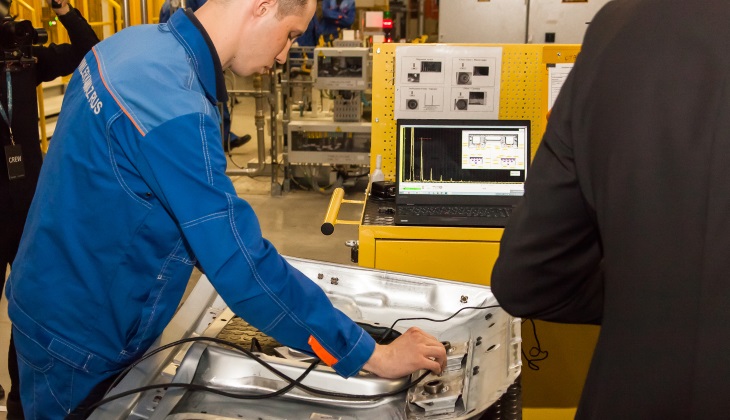
Окрашенный каркас кабины поступает в цех, где действуют строгие правила чистоты. Каждый входящий должен надеть комбинезон, плотно закрывающий руки, ноги и голову. Применяются самые современные технологии: линия окраски знаменитой марки Durr. Первый этап – катафорезное грунтование с погружением в 12 ванн. Внутри ванны кабина проводит 60 секунд. Самая интересная стадия – окраска по схеме «мокрым по мокрому», то есть на ещё не высохший грунт наносится краска. Этим экономится время и деньги. Существует 8 основных и 20 специальных цветов, а за месяц можно подобрать и индивидуальный оттенок. Вентиляция в окрасочной камере выполнена с применением фильтров из бумаги и картона, которые задерживают частицы краски.
Изношенные фильтры уничтожают сжиганием. Такая методика менее вредна для природы по сравнению с традиционной очисткой воздуха водой и снижает затраты. После этого кабина отправляется в печь для сушки. В процессе туда периодически помещают контрольную кабину, наполненную датчиками температуры, чтобы получить полное представление о ходе сушки. Проверка качества окраски выполняется под ярким светом в специальной камере, после чего на часть сварочных швов вручную, при помощи пистолета и кисти, наносится герметик.
Готовые каркасы поступают либо на грузовик КамАЗ, либо на линию сборки «Мерседесов». Изготовление кабины и качество её одинаковы как для российской, так и для немецкой модели. КамАЗ планирует устанавливать кабину на свои автомобили в течение 15-20 лет.
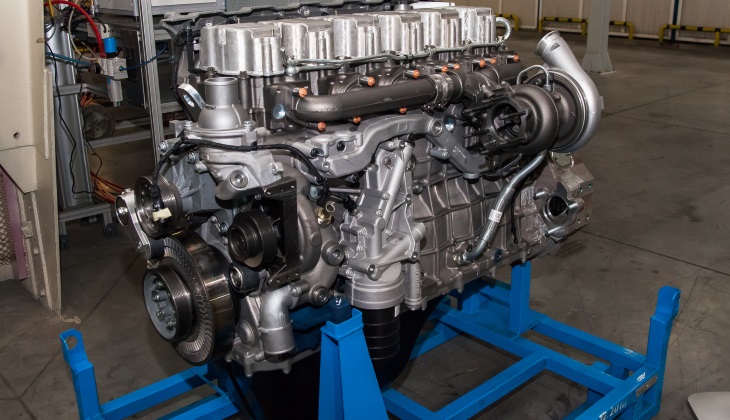
На заводе двигателей применяют другой подход. Рядом со сборочными линиями «Камминсов» и камазовских «восьмёрок» появилась новая линия для нового рядного шестицилиндрового двигателя КамАЗа-54901. В отличие от завода каркасов, здесь не стали использовать роботов, а подробно описали действия операторов, чтобы избежать ошибок. Компьютер сообщает человеку, какой инструмент взять, куда поставить деталь и с каким моментом затянуть крепёж. После операции информация о ней сохраняется в компьютере, поэтому о собранном двигателе будет известно всё.
Производители оборудования — Siemens, Thyssenkrupp, Atlas Copco. Конвейер пока короткий, поэтому на каждом посту выполняется несколько операций. Запустили выпуск чуть более семидесяти двигателей, во втором полугодии планируют выйти на мощность 200 моторов в месяц и достичь показателя 1000 штук к концу 2019 года. Планируется удлинить линию, уменьшить количество операций на каждом посту и увеличить выпуск двигателей. В проекте предусмотрено производство 12 000 двигателей в год, но обещают нарастить мощности по необходимости.
Двигатель также интересен. КамАЗ вместо покупки лицензии или копирования выбрал разработку нового агрегата совместно с компанией Liebherr. В качестве основы послужил шестицилиндровый рядный мотор Lieherr D946, но его существенно переработали, в первую очередь, для облегчения. Исходный двигатель предназначался для строительной техники и не особо заботился о лишнем весе. В результате получился мотор на чугунном блоке с мокрыми гильзами и чугунными четырёхклапанными отдельными головками. Всё для надёжности и ремонтопригодности.
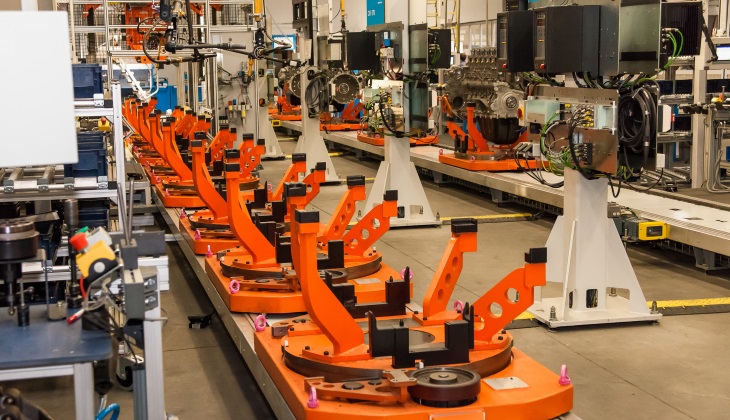
В отношении надёжности производитель гарантирует ресурс полутора миллионов километров и интервал между сервисами – сто пятьдесят тысяч километров или год. Последнее применимо к эксплуатации на дорогах категории «А», то есть магистралях, для которых и создан данный автомобиль. В более сложных условиях обслуживать транспортное средство придётся чаще. Выхлоп соответствует стандарту Евро-5. Локализация производства очень обширная и охватывает всё кроме топливной системы и турбины.
Камазовский Р6 – это семейство двигателей, части которого унифицированы и различаются прошивкой блока управления. Диаметр цилиндра и ход поршня одинаковы: 130 и 150 мм соответственно (объём 11,946 л). Мощность и крутящий момент варьируются в зависимости от модификации. Самая младшая (910.14) выдаёт 380 л. с. при 1900 об/мин и 1715 Нм при 1300 об/мин, старшая (910.10) – 550 л. с. и 2540 Нм при тех же оборотах. Существует ещё одна модификация, отличающаяся двумя работающими последовательно турбинами для достижения около 700 сил.
Успехи КамАЗа нельзя не приветствовать. Несмотря на то что модель 54901 использует каркас кабины от «Актроса» – современную и качественную кабину – он дополнен оригинальными внешними панелями и собственным интерьером. Его движущей силой стал разработанный заново двигатель, производство которого осуществляется в России. Уверены, что развитие модели будет только позитивным!